Set up designed to study the connection procedure and testing procedure of electric 3 or 4 wheeler set up using various components of electric vehicle like battery , EV.Motors , drive etc , Set up consists of
Control Panel ( with Drive, battery, charger etc)
Controller
- Type : MOSFET based Controller
- Input Voltage : 48-60VDC
- Maximum Current : 30A
Battery
- Type : lithium ion battery -LPF
- Voltage : 60v
- Power/Current : 18Ah
- Features : in built Smart BMS with PC interface Software and Bluetooth-Mobile App software -optional features.
Charger
- Type : MOSFET-based Charger
- Input Voltage: 170-250VAC
- Output Voltage: 62V
- Charging Current: 5A
- Charging Time : 4-5 Hour
- Features : Led's for status indicator
Panel
- Powder coated M.S Panel with diagram Stickered front panel to fix the Above Motor, controller and Battery and also to fix the below mentioned components
- Steering with Pedal Accelerator for speed control
- F/R selection switch, Left/Right indicator switch with Lamp
- Head light switch with Lamp, Horn switch with buzzer
- Brake control lever(optional)
- Digital LCD-indicator, To indicate
- Speed in KM/H
- Motor Speed in Rpm
- Left indicator status
- Right indicator status
- Head light Indicator status
- ON/OFF Switch with Key
- DC-DC Converter for Light (48V TO 12V, 10A)
- Necessary Banana terminals provided for motor, Battery, Controller input and outputs terminations for external patching.
- Panel Meter for Battery voltage and Current
- Necessary terminations for controller control signal (like hall sensor, indicator, throttle) output and inputs for external patching.
- Necessary Fuse and MCB provided for battery, Motor
Features
- Provision / Facility to Interface with External IGBT Power Module and Controller set up (FPGA/MATLAB/DSPIC etc)- for Motor control and testing
Optional Features
- PC Software for BMS -Smart Battery (OP2)
- Blue tooth Mobile app-connectivity for BMS -Smart Battery (OP3)
Possible Experiments
- Study and testing of speed control of Hub Motor used in two wheelers
- Study and testing of 3/4 wheeler control components functions (pedal Acce function, F/R switch function, Left/Right indicator switch function, Head light switch function, Horn switch function, Brake control lever function, Digital LCD-Indicator function etc)
- Study and Testing of battery charging and discharging - BMS system using PCSoftware and Mobile blue-tooth App (User will provide computer/Mobile)- optional features
The performance of this model could even better than the performance of benchtop oscilloscope. It has 4 analog channels, 1GSa/s real-time sampling rate, 2mV-10V/DIV input sensitivity, and 250MHz bandwidth. It is powered by USB2.0 Interface, plug and play device with small size which is easy for carrying. High cost performance, pass/fail test, resourceful trigger function, dynamic cursor tracking, waveform record and replay function
Six Phase Permanent Magnet Synchronous Motors - Order Code - EV46014M
• Voltage:60V
• Power: 1KW or 3KW (Optional)
• Speed: 2500 RPM
• Feedback: 3 numbers of Hall sensor
• Differential setup:10:1 Gear Ratio Fitted with stand and Tire, drum
Optional: Pc Based Measurement And Acquisition System For Motor Voltage And Current : Order Code - EV-DAQ
For more Information Click heare
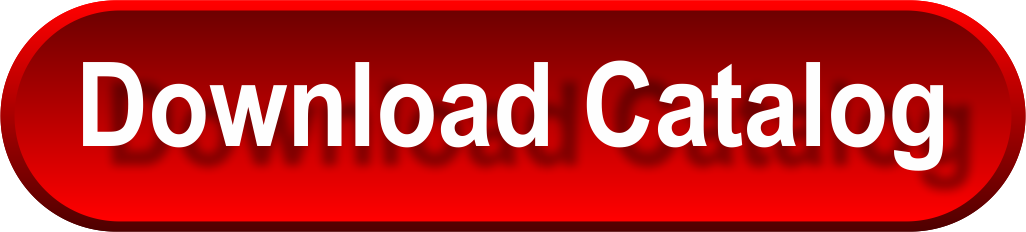